Flexographic Labels
PRINTED LABEL MARKETING COMMUNICATION SOLUTIONS
Flexographic Labels
Flexographic printing is ideal for high-volume, long-run jobs with a need for speed, versatility in substrates, and inline finishing. It is a versatile commercial printing method suitable for various materials, including paper, plastic, film, and more. It is favored for its cost-effectiveness, efficiency, and adaptability, making it an ideal choice for producing large volumes of labels and flexible packaging.
Applications include: cereal boxes, bottle labels, potato chip bags, frozen food packaging, corrugated boxes, newspapers, grocery bags, folding cartons, gift wrap, and tissue paper.
Flexography also excels in printing on non-porous surfaces like metallic films and can operate at speeds of up to 2,000 linear feet per minute. This process uses a flexible printing plate to produce high-quality prints and allows for the incorporation of decorative elements, such as special substrates, unique coatings, or inline cold foil with embossing.
Benefits of Flexographic Printing
High-Speed Production
Flexographic printing is known for its ability to run at high speeds. This makes it highly efficient for large-scale production runs, where speed is a critical factor.
Cost-Effective for Large Volumes
Flexo printing is particularly cost-effective for high-volume production.
Versatility in Substrate Compatibility
Flexography can print on a wide range of materials, including non-porous surfaces like plastic films, metallic foils, and other specialty materials. This versatility makes it ideal for packaging applications, labels, and other flexible materials.
Longer Runs and Durability
The printing plates used in flexographic printing are durable and can be reused for long runs, making it a reliable option for consistent, high-quality output over time.
Inline Finishing Capabilities
Flexographic presses can incorporate various inline finishing processes, such as die-cutting, laminating, varnishing, and foil stamping. This ability to complete multiple processes in a single run increases efficiency and reduces turnaround times.
Superior for Certain Specialty Applications
Flexography is well-suited for printing on materials that require specific inks, such as water-based or UV inks, and can handle specialty coatings or effects that are more challenging for digital printing.
Considerations
Setup Time and Costs
Flexographic printing requires more upfront setup time and costs (e.g., creating plates) compared to digital printing, which can be more advantageous for shorter runs or projects requiring frequent changes.
Quality and Detail
Digital printing often excels in producing highly detailed images, especially for projects requiring frequent changes or short runs, where setup costs would otherwise be prohibitive.
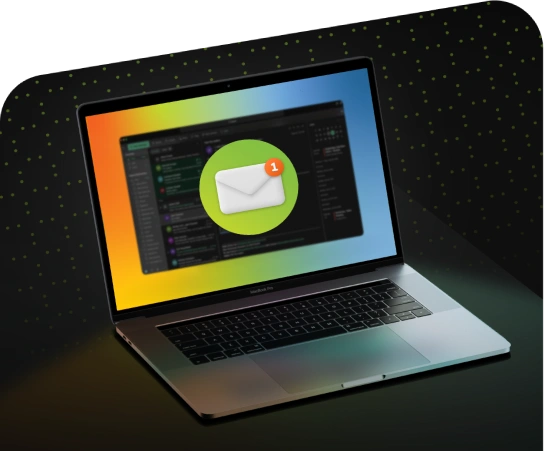
Join our email list
Stay up to date on the latest Meridian news, products, and promotions.
Related blog posts
Check out our articles below or visit our blog page to read more!
Meridian and Lux Press Group Take Home Three Awards at the 32nd Annual FSEA Gold Leaf Awards
We’re thrilled to share that Meridian and Lux Press Group were recognized with three awards at the 32nd Annual FSEA Gold Leaf Awards, a premier industry event that celebrates innovation in print embellishment, foil stamping, laminating, and specialty finishing. With...
Cardo Inflatable Edgephones
When Cardo Systems reached out with a bold idea—to turn their Edgephones into a larger-than-life inflatable—we were ready to make it happen. It was the kind of high-visibility moment their brand deserved—and exactly the kind of challenge we love. From Product Photos...
Employee Appreciation Day
Showing Your Team Love—Every Day Employee appreciation isn’t just a one-time event—it’s an ongoing investment in your team’s success. When employees feel valued, they’re more engaged, productive, and loyal to their workplace. One of the simplest yet most effective...